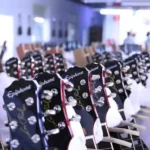
Epiphone Factories
Epiphone, a name synonymous with quality musical instruments, especially guitars, has a rich history intertwined with innovation, artistry, and craftsmanship. The journey of this brand traces its roots through various factories, locations, and ownerships. Here’s a comprehensive insight into Epiphone’s factories and their significance in the company’s storied past.
Table of Contents
1. Beginnings in Smyrna (1873-1903)
The story of Epiphone begins in the Ottoman Empire, in the town of Smyrna (now İzmir, Turkey). Anastasios Stathopoulo, a Greek luthier, crafted traditional stringed instruments like lutes and fiddles. This marked the genesis of the Epiphone craftsmanship that continues to evolve to this day.
2. Moving to New York (1903-1953)
In 1903, Anastasios migrated to the U.S., setting up a small workshop in Manhattan, New York. The shop’s focus was primarily on manufacturing mandolins, which were immensely popular during that era. The name “Epiphone” hadn’t yet been adopted. It was derived later, from Epi (a nickname for Epaminondas, Anastasios’ son) and the Greek word ‘phone’ (voice). This was a tribute to Epi’s leadership and the sonic output of their instruments.
The 1930s was a pivotal decade for Epiphone, marking its transition from a modest musical instrument maker to a major contender in the American market. This period was marked by innovation, expansion, and intense competition, particularly with Gibson. The factories from this era reflected the brand’s ambition, technological advancements, and the changing dynamics of the musical world.
By the early 1930s, Epiphone had outgrown its original Manhattan workshop and set up shop at 142 West 14th Street, New York City. This wasn’t just a production facility but also acted as the company’s headquarters.
Facility Features:
- Size and Layout: The factory was larger, allowing for increased production capacities. The space was designed to facilitate an assembly-line approach, improving efficiency.
- Craftsmanship: The facility was equipped to handle the crafting of a wide range of instruments, from banjos, which were in vogue during the early part of the decade, to archtop guitars, which became the rage by the mid-1930s.
The 1930s was a decade of innovation for Epiphone, and the factory was the nucleus of these advancements.
- Masterbilt Series: Introduced in the mid-1930s, this line of archtop guitars directly challenged Gibson’s supremacy in the market. The factory was equipped to produce these instruments with precision, ensuring high-quality sound and finish.
- Acoustic Research: The factory had dedicated areas for acoustic research, where craftsmen and engineers could experiment with designs, materials, and bracing patterns to enhance the sound quality of their guitars.
A significant factor behind the success of Epiphone during the 1930s was its skilled workforce. The craftsmen at the New York factory were often European immigrants with a deep-rooted understanding of traditional luthiery. They brought with them techniques and skills that contributed to the unique character of Epiphone instruments.
The 1930s was also the era of the Great Depression, which inevitably impacted the musical instrument industry. Epiphone, however, managed to weather the storm better than many of its competitors, thanks to its innovative designs and aggressive marketing strategies. The factory played a pivotal role in ensuring production met demand without compromising on quality, even during these challenging times.
3. Epiphone Gibson Factories USA (Since 1957)
After the death of Epi Stathopoulos in 1943, the company faced various challenges, leading to tensions between the family members. As a result, the company was put up for sale. In 1957, Chicago Musical Instrument Company (CMI), Gibson’s parent company, acquired Epiphone.
Under Gibson’s leadership, Epiphone’s production was initially moved to a Gibson plant in Kalamazoo, Michigan. The merger saw the amalgamation of Gibson’s renowned design prowess with Epiphone’s legacy, producing instruments that carried the essence of both brands.
4. Epiphone Japan Factories (1970s)
The 1970s marked a shift in guitar manufacturing, as many companies, including Gibson and Fender, started moving production offshore to reduce costs. Epiphone too was part of this wave.
Initially, production was moved to Japan. These Japanese-made Epiphones, especially from the Matsumoku factory, are considered to be of high quality and are sought after by collectors.
The period during which Epiphone started producing guitars in Japan is pivotal in the company’s history. This move was largely in response to changing economics, shifts in consumer preferences, and the emergence of Japanese manufacturers as significant players in the guitar market.
During the late 1960s and early 1970s, Japan emerged as a major center for guitar manufacturing. Japanese factories began producing high-quality guitars, rivaling American counterparts. Brands like Ibanez and Yamaha became internationally recognized, which drew the attention of American companies.
Matsumoku is arguably the most well-known factory associated with Epiphone’s Japanese era. Located in Matsumoto, Nagano, Japan, Matsumoku initially made wooden cabinets for sewing machines before transitioning into guitar manufacturing.
When Epiphone decided to shift production to Japan in the 1970s to reduce costs, Matsumoku became a key partner. Guitars produced in the Matsumoku factory are now considered to be among the best Epiphones ever made. These instruments are known for their quality craftsmanship, often being compared favorably to more expensive American-made models.
The Japanese Epiphones from this period had their distinct character. Some models were unique to the Japanese market, while others were reiterations of classic American designs. Japanese factories, including Matsumoku, introduced innovations in terms of materials, hardware, and finishes, leading to guitars that were distinct yet still carried the Epiphone ethos.
While Matsumoku was a significant producer of Epiphone guitars, it wasn’t the only one. Several other Japanese factories were involved during this era. However, by the late 1980s and early 1990s, the focus of Epiphone’s production shifted to Korea due to rising labor costs in Japan and the increasing capabilities of Korean manufacturers.
Japanese-made Epiphones have become highly sought-after collectibles. Players and collectors recognize the quality and uniqueness of these instruments. Especially the Matsumoku-produced guitars are often praised for their build quality, tonal characteristics, and attention to detail. They represent a specific era in the guitar world, where Japan was emerging as a powerhouse in guitar craftsmanship.
5. Epiphone Korea Factories (1980s-2000s)
In the late 1980s and early 1990s, labor costs in Japan began to rise, making guitar production more expensive. Additionally, the quality of Korean craftsmanship had greatly improved, making it an attractive alternative for many guitar companies, including Epiphone.
The Samick factory, located in Incheon, South Korea, became one of the primary facilities producing Epiphone guitars. Samick, already an established name in the musical instrument industry, was producing its own guitars and manufacturing for various other brands.
Guitars produced at the Samick facility during this period are known for their consistency, quality control, and affordability. This partnership helped Epiphone maintain a reputation for delivering good quality guitars at a more accessible price point.
Korean Epiphones introduced several models and variations that became popular. While they produced many of the standard models you’d associate with Epiphone, the Korean era also saw the birth of models and variations that were exclusive to this period. Some of these guitars have since gained a cult following and are sought after in the second-hand market.
One of the distinct features of Korean-made Epiphones is their serial numbers. These numbers often start with a letter, which typically identifies the factory where the guitar was made. For instance, guitars with serial numbers beginning with “I” were produced at the Saein factory in Incheon. Over the years, several Korean factories, such as Unsung, Peerless, and Sunbo, also produced for Epiphone, and each had its own prefix.
While the quality and consistency of Korean-made Epiphones were commendable, the rise of other Asian manufacturing hubs, especially China, prompted another shift. By the early to mid-2000s, a significant portion of Epiphone’s production had moved to China due to even lower production costs and the capacity to handle large-scale production.
However, Korean factories continued to produce certain models and remained integral to Epiphone’s global manufacturing network.
Korean factories played an essential role in Epiphone’s history, bridging the gap between the Japanese era and the subsequent transition to China. Guitars from this period are often praised for their balance between quality and affordability, reflecting the advancements in Korean craftsmanship and the evolving global dynamics of guitar manufacturing. For many guitar enthusiasts and players, Korean-made Epiphones hold a special place for their unique blend of heritage, quality, and value.
6. Epiphone China Factories (Since 2000s)
The transition of Epiphone production to China, beginning in the early 2000s, represents another significant phase in the brand’s history. This move was influenced by global economic factors, production capabilities, and the evolving landscape of the guitar industry.
As was the case with the earlier move from Japan to Korea, shifting production to China was largely an economic decision. China’s burgeoning manufacturing industry offered competitive labor costs and an infrastructure conducive to large-scale production. These economic incentives made it possible for Epiphone to produce instruments at a reduced cost, thereby making them more accessible to a broader audience.
One of the primary facilities for Epiphone’s production in China is the Qingdao factory. Located in the coastal city of Qingdao in Shandong province, this factory is unique because it is wholly owned by Gibson, Epiphone’s parent company. Having a proprietary facility ensures that quality control measures can be strictly enforced, leading to consistently high-quality instruments.
The production capacity and efficiency of Chinese factories allowed Epiphone to introduce a wider variety of models and finishes. This period saw the release of several unique Epiphone models, many of which were exclusive to the Chinese production era. The brand was able to experiment with diverse designs and cater to various musical genres and player preferences.
One of the initial concerns when major brands started manufacturing in China was quality consistency. However, as the years progressed, Chinese factories, including those producing Epiphones, greatly improved their quality assurance processes. Many musicians and critics noted that the quality of Chinese-made Epiphones was on par with, if not superior to, their Korean and Japanese predecessors in certain aspects.
The Chinese factories employed local craftsmen trained in the tradition of instrument-making. Collaboration between these artisans and Epiphone’s design team from the U.S. led to a unique blend of East-meets-West in terms of craftsmanship, resulting in instruments that maintained Epiphone’s legacy while infusing fresh characteristics.
One challenge Epiphone faced with Chinese production was the rise in counterfeit guitars. The likeness of some of these counterfeit models to genuine Epiphones was often strikingly close, leading the company to implement stricter serial numbering and authentication methods.
While China remains a significant production hub for Epiphone, the brand, like many others in the industry, has started diversifying its manufacturing locations. This diversification includes a return to producing certain premium models in the United States and expanding production in other Southeast Asian countries like Indonesia.
The China period of Epiphone’s production history has been marked by both challenges and achievements. It stands as a testament to the brand’s adaptability in navigating global economic shifts and its commitment to producing quality instruments across different production landscapes. Over time, Chinese-made Epiphones have secured their place in the brand’s legacy, loved by many for their blend of quality, affordability, and innovation.
7. Return to the USA (2020s)
Epiphone’s return to U.S. production is significant for the brand, symbolizing a full-circle journey from its early American roots to global manufacturing and back to its homeland.
Epiphone, as a brand, originated in the USA in the early 20th century. Its return to American production is a nod to the brand’s rich legacy and heritage. This move resonates with many guitar enthusiasts and collectors who value American craftsmanship and the historical significance of instruments made in the USA.
The USA-made Epiphones are positioned as premium models within the brand’s lineup. By producing in the USA, Epiphone can harness advanced manufacturing techniques, high-quality materials, and skilled craftsmen, ensuring these guitars are of top-tier quality. These models are often distinguished by superior tonewoods, hardware, and finishing touches compared to their overseas counterparts.
With the reintroduction of U.S. production, Epiphone also ventured into limited edition releases and potential custom shop offerings. These instruments often incorporate unique features, designs, or collaborations that set them apart from standard models.
The demand for American-made guitars remains strong, especially in the premium segment of the market. Many players believe that USA-made instruments offer a unique tonal character, build quality, and overall playability that’s hard to replicate elsewhere. By producing guitars in the U.S., Epiphone is catering to this demand and distinguishing itself from competitors.
Naturally, producing in the USA comes with higher labor and material costs. As a result, American-made Epiphones are priced higher than those made in Asia. However, for many consumers, the added cost is justified by the perceived increase in quality, the prestige of owning an American-made instrument, and the connection to Epiphone’s storied past.
The guitar community’s response to Epiphone’s return to the USA has generally been positive. Many players and collectors appreciate the brand’s commitment to its roots and the effort to produce high-quality instruments in the USA. While these guitars cater to a specific segment of the market, they have found their niche among those who value American craftsmanship and the Epiphone legacy.
Epiphone’s decision to return to American production is both a strategic business move and a nod to the brand’s illustrious history. By producing premium models in the USA, Epiphone bridges its past with the present, offering instruments that resonate with the brand’s legacy while meeting the demands of modern players. This move underscores the brand’s adaptability and commitment to quality, further cementing its place in the annals of guitar history.